We can produce produce high-quality deformed steel bars with our state-of-the-art facilities.
We have introduced high-speed, high-precision block mills, full-tandem H-V continuous mill, and continuous rolling control technology.
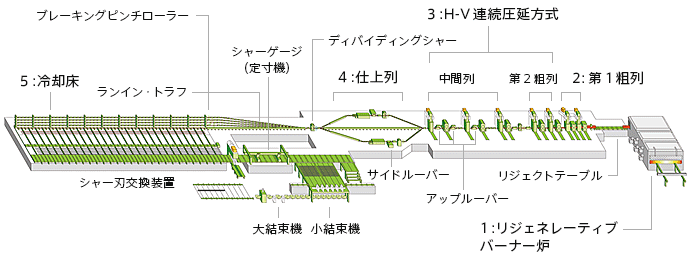
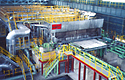
Adopted LS light oil regenerative burner furnace for the first time in Japan. By alternately switching between the left and right burners (approximately 40-second intervals), the atmospheric temperature inside the furnace is made uniform, minimizing the temperature variation inside the material bar (conventional furnace 40°C → 20°C) and reducing the variation in the dimensions of the product bar.
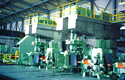
The compact mill rolling mill can be narrowed to 1,250 mm between the center cores of the stand, and is stabilizing operation by strongly reducing the area by pressing and minimizing jamming troubles.
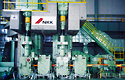
HV full tandem arrangement (H: horizontal, V: vertical rolls are alternately arranged in a straight line) from rough to intermediate rolls to achieve high-precision, high-speed rolling and minimize operational troubles.
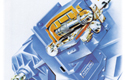
High-speed, high-precision block mills, which are also used for wire rod rolling, are arranged in 4 rows x 2 rows, and the material divided into 2 by single slit rolling is finished rolled one by one.
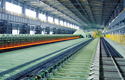
A 110m-long rake-type cooling floor prevents products from bending by rotating and feeding them sideways for cooling.
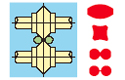
A roll of material is rolled into a spectacle shape, slit into two, and then finished rolled. This rolling method has reduced the number of stands by two.